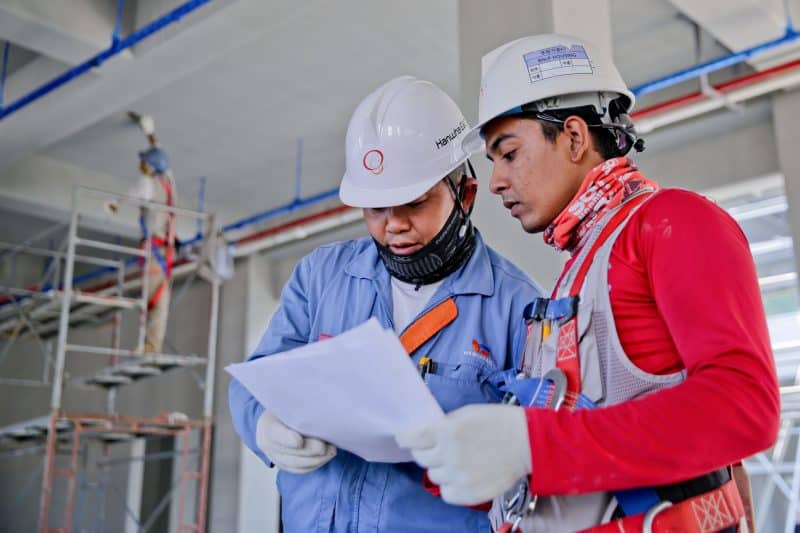
Facility management tasks are performed differently by everyone based on local conditions and requirements. Hospitals, malls, or office buildings are operated differently. This difference is true for both processes and managed devices. Moreover, we are not talking about small differences.
The Operational BIM approach represented by OrthoGraph® allowed the use of custom data sets from the first moment, which were developed at the beginning of each project during a 3 day consultation and customization phase in collaboration between partner, client and OrthoGraph®. Anytime later client was able to extend the data to be collected within a limit, e.g. additional photos, data fields attached to the inventoried items. Unfortunately, fixed lists were not among these extension choices, and also changing already existing properties was impossible. This ruled out the possibility of one of the most important data cleaning features, using fix value choices, without the help of OrthoGraph.
The most recent OrthoGraph® version simplifies the procedure of creating custom project templates a lot, as custom data sets, fixed lists will be available to all customers without manufacturer’s intervention. What’s more: as the needs, and served tasks, workflows are changing and expanding continuously, anyone with the right authorization can change these data sets later, also without the involvement of the developer or the introductory company.
We shouldn’t forget about Enterprise Level integration too. When defining fixed lists to control data quality, then OrthoGraph supports key-value pairs. In this case the values are shown and readable by human, and the related keys are communicated via the integration to external systems.
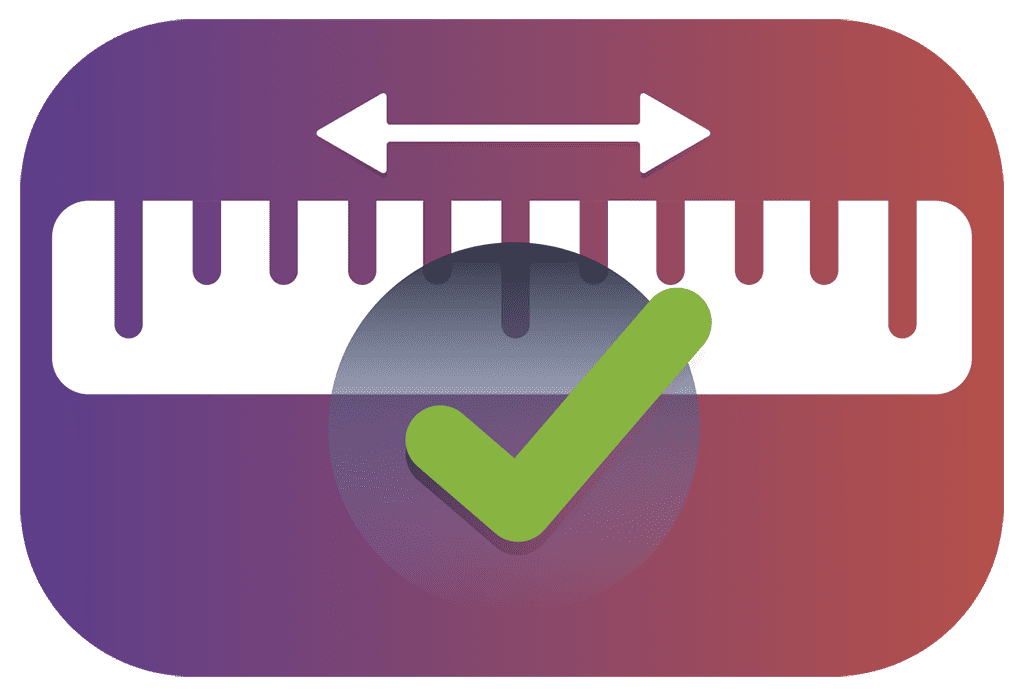
The project implementation and surveying process is as follows:
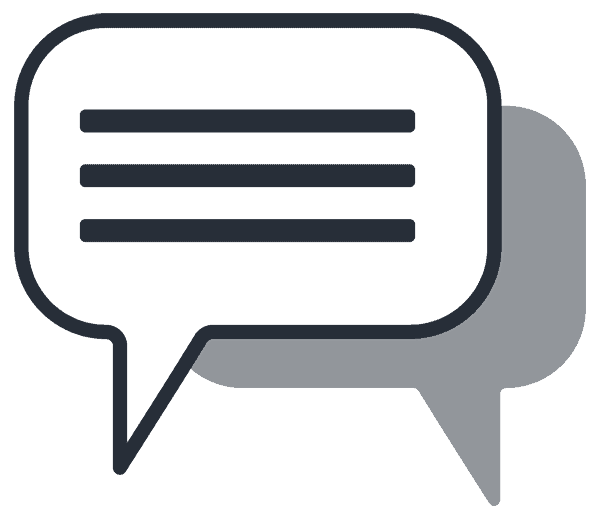
1.
Customer and implementer company discusses and identifies the goals expected to reach with the Operation BIM. This might be the most important step in this process.
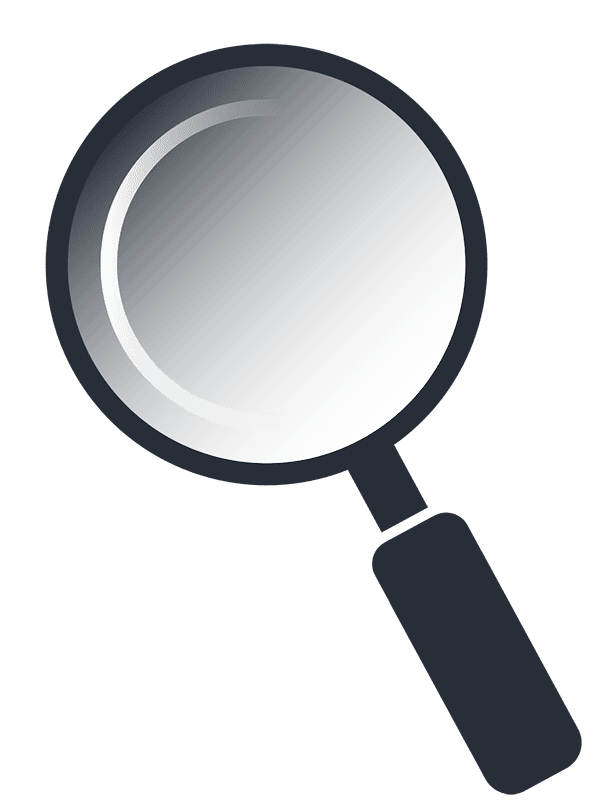
2.
They define together the data sets to be surveyed:
• asset types to be inventoried
• room, opening and asset properties
• fixed list entries, default values and mandatory fields
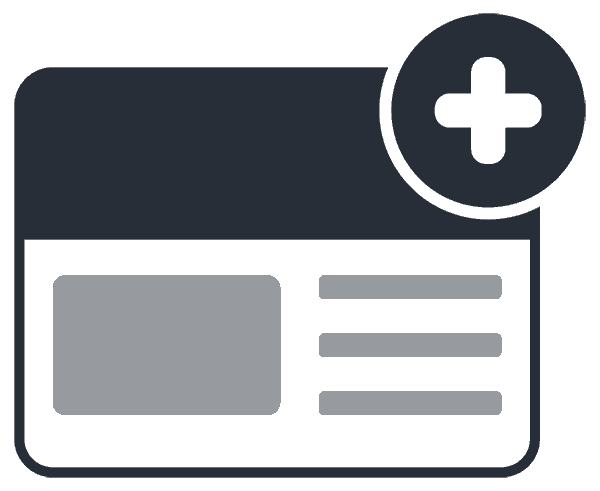
3.
The surveying firm creates the custom project template.
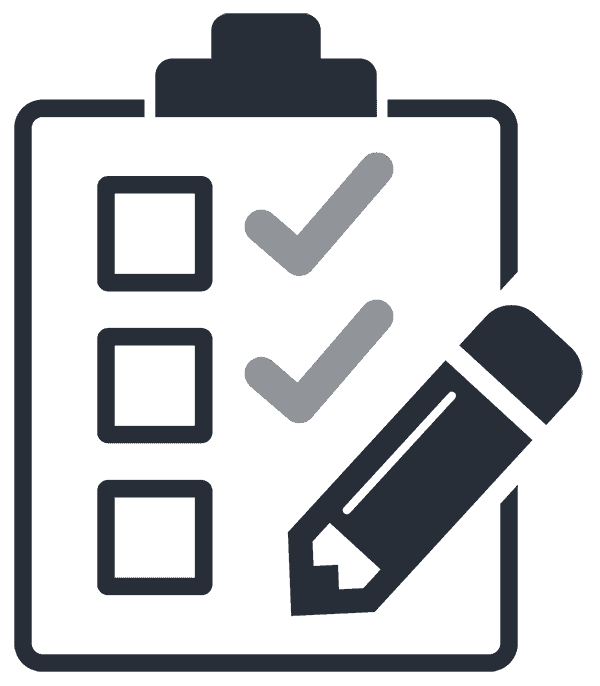
4.
The surveyor company evaluates the project template by surveying a couple of typical “showrooms” involving the responsible decision-makers on site as observers (this helps to assess the time and energy needed to keep the model up-to-date later on).
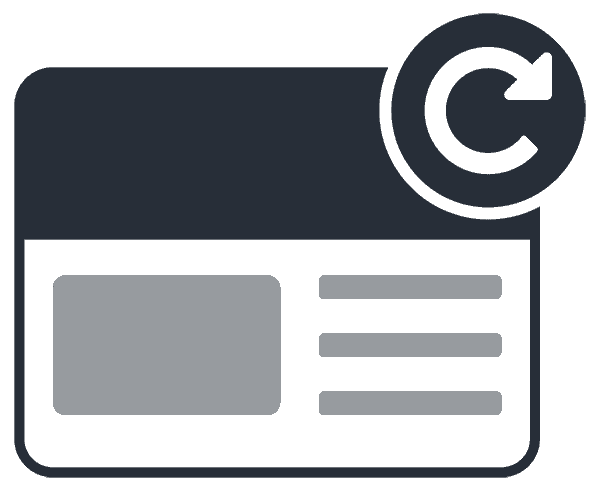
5.
At this point typically the extent of data set is reduced, and also other stakeholders and areas (e.g. IT) get involved, which changes are implemented in the project template by the implementation partner.
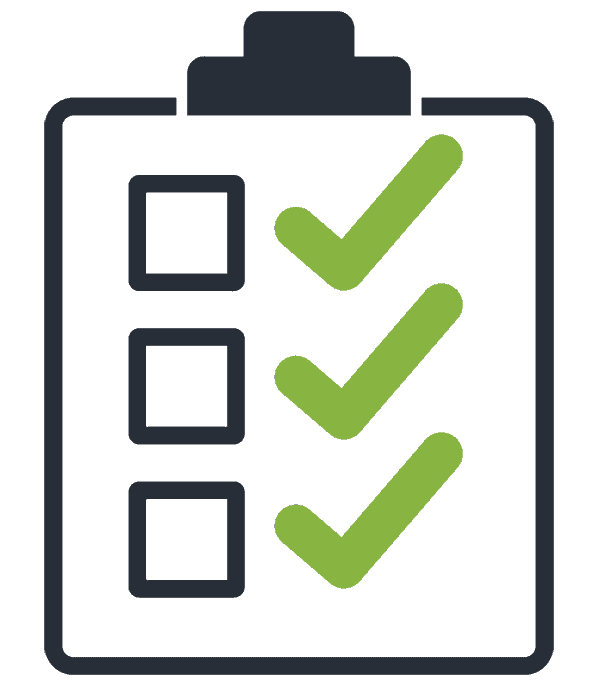
6.
The surveying company carries out the full survey project (including the repeated survey of the showrooms),
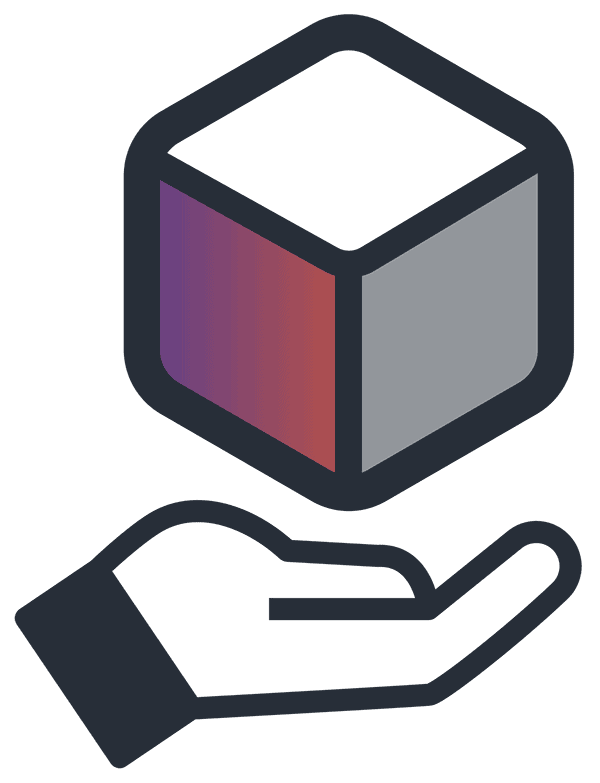
7.
The surveyed model is handed over to the client. This can be also made gradually during the project, so they can follow and inspect the data quality.
This all means that the already fast surveying processes can be even faster, and there is no building that cannot be surveyed and inventoried in a few weeks with high accuracy, and with digital quality assurance.
Furthermore all this data can become a part of the everyday operation ensuring that the digital twin of the building will contain every building knowledge instead of storing them in the heads of the operational crew. This improves operational performance while reduces the risk of data loss due to the fluctuation of employees.
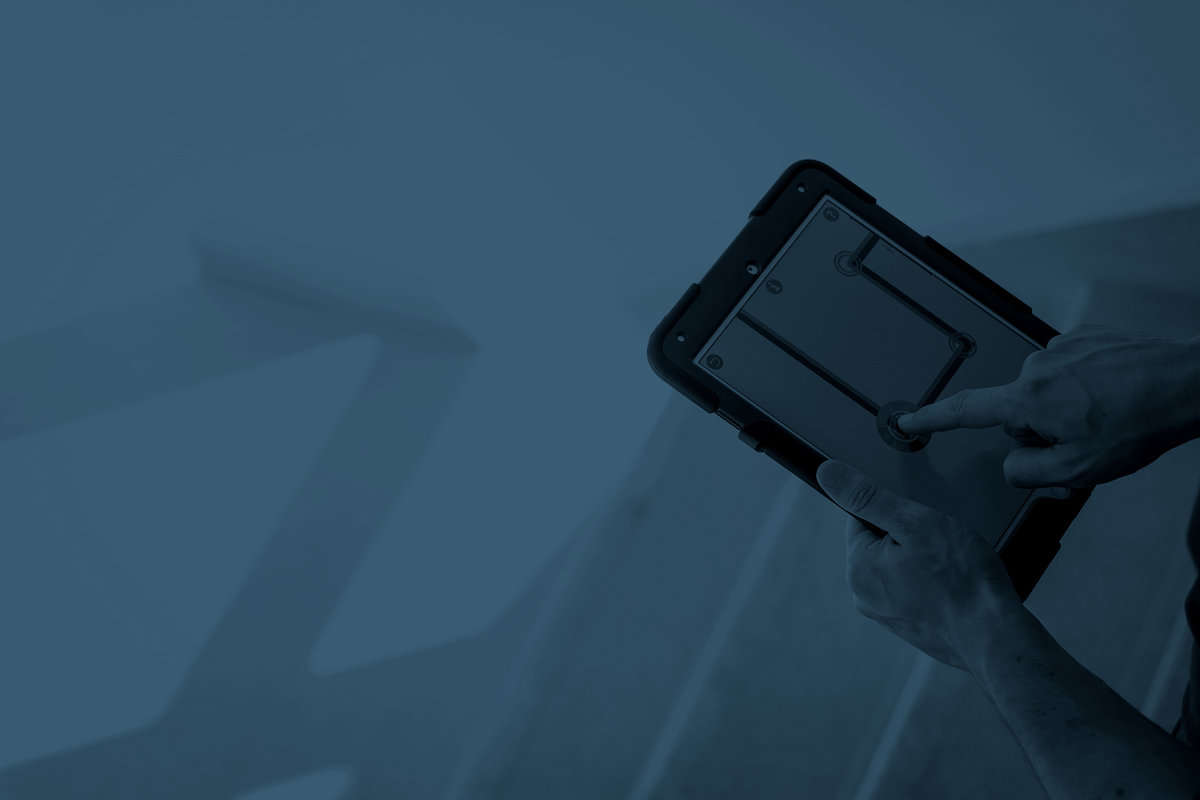
Recent Comments