Facility Management
New property construction,
development phase
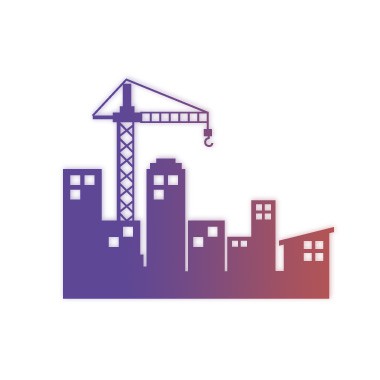
Settling accounts with subcontractors on the basis of precise data
Expected cost: 0.1% of investment cost
Products used: Leica BLK360, OrthoGraph Enterprise
If usage of the OrthoGraph and Leica BLK360 systems is started at the development stage, significant savings can be achieved already at that time with the knowledge of the precise, measured values. This is because, on one hand, by using the surveyed models settling accounts with subcontractors can take place on the basis of precise data, and, on the other hand, the building models created can be used later on directly in the facility management system as source data.
Using the periodical laser measurements performed and repeated with the Leica BLK360 the various construction phases can be easily identified and the entire building documentation is available in a layered structure. Additionally this data may serve as documentary evidence when settling accounts with subcontractors.
Surveying and registering the built-in equipment
Expected cost: 0.025%
Products used: OrthoGraph Enterprise
All built in devices, building engineering elements and all equipment that may possibly be covered at a later stage, such as by false floors and ceilings, can be registered during construction. When an equipment is recorded this does not only mean that dimensions and position are recorded, it includes other parameters too such as serial number, guarantee period, capacity, type number and even a photograph of it.
This information is automatically available in the connected CAFM and CMMS system, already at the moment of occupation.
These same elements included in the building model can be linked to any other system, a building automation system, for instance.
Construction surveys can prevent many problems and expenses later on
Expected cost: 0% in the case of surveys performed during the development stage
Products used: Leica BLK360
It should be noted that as a consequence of the detailed documentation any reconstruction or repair work taking place in a later operation phase can be supported with the Leica BLK360 system with the ability to perform any subsequent measurement on the intelligent panorama photos made during the construction phase. This way plumbing connections and electrical fittings can be located and accessed with minimum wall demolition. In the same way, damage can be prevented with them in the case of damage caused when the under-floor heating systems are drilled through when installing a simple door frame for example, in other words the safe work-positions are located using precise measurements made in the point cloud before any work in covered areas is carried out.
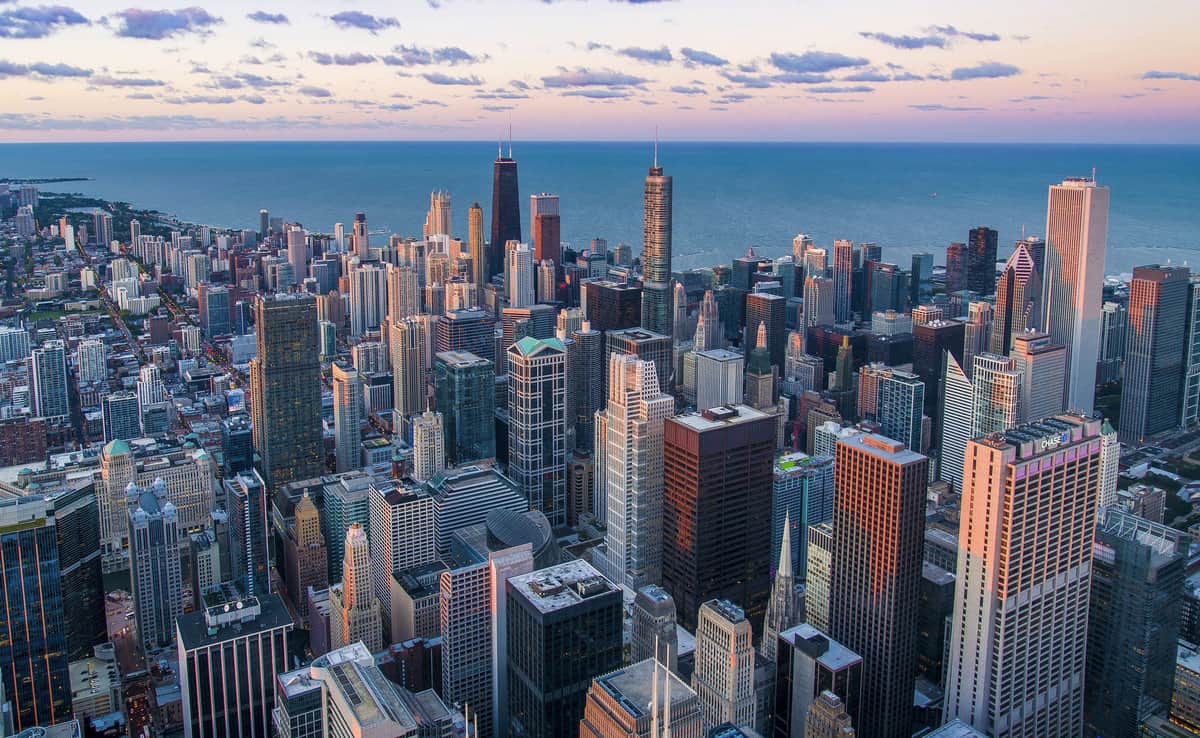
Several percent increase in value of property sales and valuation
Expected cost: 0%, if the model surveyed during the development is used, otherwise 0.025% of the investment cost (an even smaller part of the sale value), as long as a dedicated survey is carried out before occupation
Products used: Leica BLK360, OrthoGraph Enterprise
In the course of the sale of a property, the handover of the property also involves its detailed documentation. This represents value and a guarantee for the buyer, because the condition at handover is recorded. Today, if any implementation building documentation is available at all, it is usually non-reusable and typically deviates by as much as 5-10% from the actually realised situation. In the case of the use of the OrthoGraph system the emphasis is on surveying speed, the quality of the models produced, and on the ease of use of the results, in which OrthoGraph offers an unparalleled service currently unique on the market.
Leasing phase, communication and marketing tool
Expected cost: 0%, if the model surveyed during the development is used
Products used: OrthoGraph Enterprise
OrthoGraph is not there to replace desktop design programs, instead it is able to provide them with a finished condition as a data source in numerous CAD formats.
When the lease negotiations are taking place in connection with any office, shop or industrial unit, precise on-site building models can be presented at these meetings in order to confirm furnishing concepts and floor plan changes. At this time both the lessor’s agent and the client have the opportunity to jointly interpret not only the floor plan easily, but also the desired furnishings with the help of the 3D model. The building model jointly established and agreed on can be shared immediately with the client in the form of a link that can be viewed later on simply using a web browser, and the professional interior design plans can be drawn up in parallel with this.
Another important advantage of the use of OrthoGraph is that area data can be produced at any time, even during meetings with clients, including painted area data, door and window area data, in other words good cost estimates and utilization efficiency estimates can be made even during the negotiation phase.
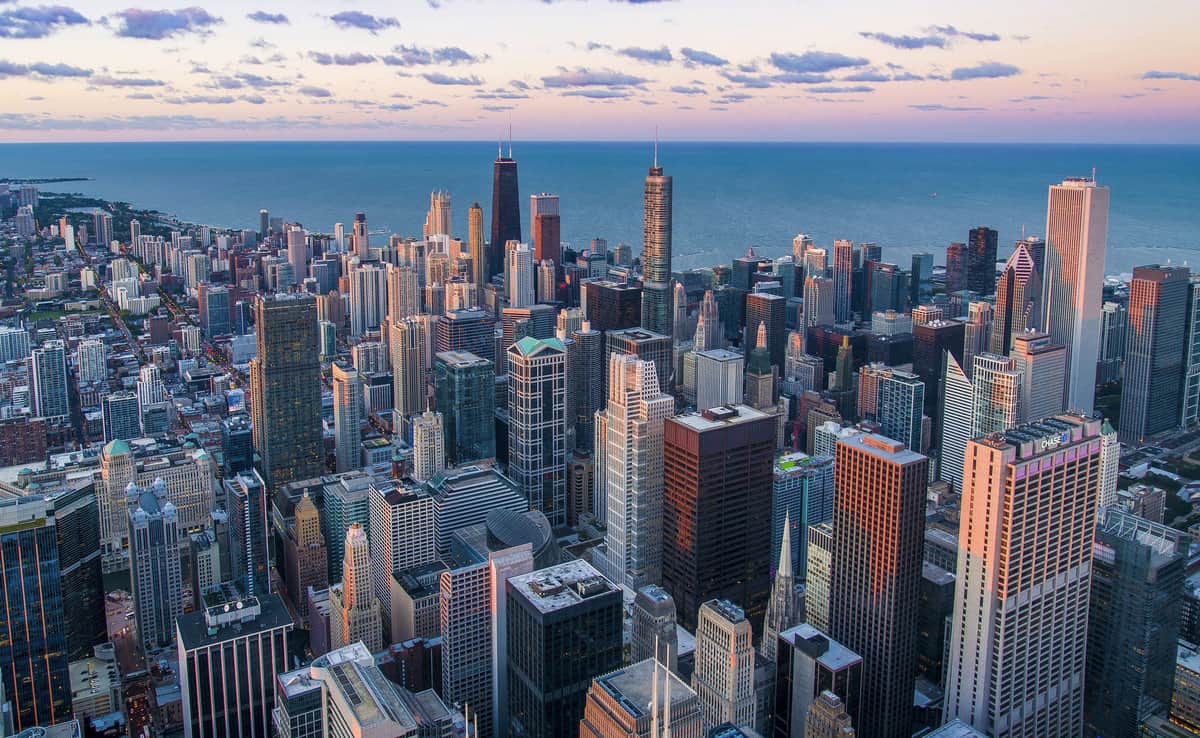
Property survey at occupation
Expected cost: 0.1% of the investment cost if the model surveyed in the course of the development is not available
Products used: OrthoGraph Enterprise
Surveying an existing building can bring about significant savings if the building was not surveyed during construction, i.e. precise floor plan information is not available. These models can provide definite data for the leasing, utilization and maintenance management of buildings, in addition, the information is not only stored on paper in a warehouse, but is available immediately in the office during operations, and even on-site. Access to data takes place directly at element level, so you don’t have to search for anything, the maintenance instructions, videos, and even guarantee documentation can be linked to the surveyed and managed elements.
The total savings that can be achieved by using an up-to-date property model may exceed the total investment cost of a building, with 100-300% savings being achieved over the course of a typical (at least 30-year) lifecycle of the building.
It is important to note that these savings do not only originate from the mere availability of the data, by using them, lease, operation, cleaning and other property subcontractor contracts can be concluded with better conditions, and a smaller maintenance team will be able to provide a better quality service than without the data.
Extra services can also be offered to tenants using the graphic models, which result in an increase in income in addition to a higher level of service and greater customer satisfaction. Such may include, for example, in the place of/in addition to a basic-level telephone fault reporting service, a graphic 3D model can be used to report problems. With this, tenants and the staff find it easier to report faults, the status of the reported fault can be traced directly while the maintenance personnel are notified immediately, even including automated scheduling.
The precise possibilities and advantages are detailed below:
Precise calculation and handling of leased areas
Expected cost: 0% if the floor plan of a previously surveyed building is available
Products used: OrthoGraph Enterprise, Space Management system
When leasing out property, or afterwards it is necessary to know the exact size of the area leased. The simple availability of this data makes concluding the contract faster and, if the values are precise, they can be used later on to prevent disputes.
After the entire surveyed room structure has been loaded into the CAFM system’s space management module, it also receives the calculated data, meaning the net, gross, leasable, cleaning areas, painting area and area covered by doors and windows. When carrying out these calculations the OrthoGraph system pays attention to the smallest of details, for example, it subtracts the area covered by columns from the leasable area, or the area covered by built-in furniture from the cleaning area, of course, if set in this manner during the survey.
The surveyed and calculated data are updated in the case of each plan amendment. It is this up-to-date information that forms the basis of the area management module of the CAFM system.
For each single room most CAFM systems can record who the tenant is, what contract the tenant has, the lease ratio and time interval. As a result the monitoring of contracts, their planning and account settlement becomes significantly simpler.
By using the reports made by the analysis module of the CAFM system, you can find out about contracts that are soon to expire, so they can be extended at the right time.
Precisely contracted cleaning expenses
Expected cost: 0% if the floor plan of a previously surveyed building is available
Products used: OrthoGraph Enterprise, CAFM, CMMS
The OrthoGraph system does not only calculate the area of rooms but it can also determine the area covered by doors and windows and by objects placed on the floor. This means that if the survey is performed at the appropriate standard, the application will automatically calculate the actual areas that need cleaning, from which the areas of built-in furniture, cupboards, columns, larger machines can be deducted, even automatically.
The complete cleaning plan can be drawn up and scheduled in the maintenance management module. It can be used to set the different scheduling of the individual room categories, to issue work sheets for work being done, and to check completion of the finished work and to settle accounts.
Precise data means that comprehensive subcontractor contracts can be concluded with better conditions. These apply to entire building levels or a building section of any kind provided there is a detailed cleaning plan and an accurate area information always at hand.
Accounting for renovation work on the basis of real data
Expected cost: 0% if the floor plan of a previously surveyed building is available
Products used: OrthoGraph Enterprise, CMMS, Leica BLK360
Planning renovation work demands precise floor plans. There is a real difference between cabinets just about fitting in and just about not fitting in a given space, and it also does make a real difference in that quotes and payment for work take place on the basis of the right information. If old building documentation is available, as a result of construction differences and changes made in the meantime, its data can characteristically deviate by as much as 5-10% from the real building dimensions and arrangement.
In many cases, when requesting quotes it is necessary to know the dimensions of the painted surfaces, of the wall surfaces and even of the doors and windows. The OrthoGraph system is able to supply this data immediately.
During remodeling work the electrical and other building engineering systems become accessible. It is worthwhile surveying these during any remodeling work using the Leica BLK360 laser scanner, because then every element will be measurable in the course of any reconstruction or repair work later on. By using the system, for instance: a water connection can be installed with minimal wall demolition because in the laser point cloud everything can be measured and located at a precision of greater than 1 cm. Due to this the amount of demolition and repair work can also be significantly reduced.
If OrthoGraph is the only available component, it too can be used to measure the areas and surfaces when work is being handed over, which does not only form the basis of the settlement for the work, but an up-to-date building documentation is also drawn up as a result, and so operation can continue on the basis of precise data.
By using the maintenance module all reconstruction work can be planned and scheduled, and the entire work process can be handled by using the worksheets based on measured data supplied by the OrthoGraph BIM model.
Graphic asset inventory
Expected cost: On one occasion the production of a complete graphic inventory, then keeping it up to date with the help of the maintenance personnel
Products used: OrthoGraph Enterprise, CAFM, Accounting system
In most large companies stocktaking is compulsory from time to time. With the use of the OrthoGraph system the stocktaking can be carried out on one occasion in full, graphically, in about the same amount of time required to carry out a normal, non-graphic inventory.
The completed asset inventory handles the elements linked to specific rooms as a consequence of their fixed graphic positions. This means that the asset information can be reused in numerous ways, monitoring moves means simple floor plan movements, which the maintenance personnel / move coordinators can also carry out. Due to the fact that the OrthoGraph system can handle barcodes (or even NFC chips), finding actual assets is performed simply by using a mobile application on-site. That way personnel can monitor movements significantly faster, with less investment of energy, so that the inventories are always up-to-date.
The assets have their allocated position, type and a barcode and all the information that may be required at a later date for the operation of facilities. The installation dates of the assets can be set, as can the guarantee period, manufacturer data, attached documentation and even photos and videos to assist maintenance. By the deep level of integration this information is accessible in both the OrthoGraph, and in the CAFM/inventory system resulting in users can access them and check them anywhere.
The CAFM system receives the movements from the OrthoGraph system automatically. So the movement of inventory assets can be immediately linked to the cost centers on the basis of the business branches, department or tenants coupled with the rooms. The inventory sheets can be queried from OrthoGraph from only one room level Excel file, from the CAFM system according to any breakdown; this way legal obligations can be complied with at any time by the click of a button.
Due to the fact that the data and position of the assets are available in the BIM model, this information can be used in numerous ways to support day-to-day operations.
A deatiled documentation about achievable saving using OrthoGraph and ArchiFM technologies together also mentioning the tools and way of their support:
Download here
to our Newsletter
OrthoGraph

Contact us
Contact us
OrthoGraph GmbH
Gartenstrasse 7
Zug
Switzerland
6300
+ 41 (41) 5510150
9:00-18:00 Zurich Time
USA: +1 760 933 1550
UK : + 44 (20) 34119438
Other pages
Education
Rapid Survey Concept
Orthograph for Constructions
Historical Building Survey