Technical Structure of the AIMNT System
The OrthoGraph AIMNT system is accessible via a web interface, with the central platform being the OrthoGraph Maintenance Center.
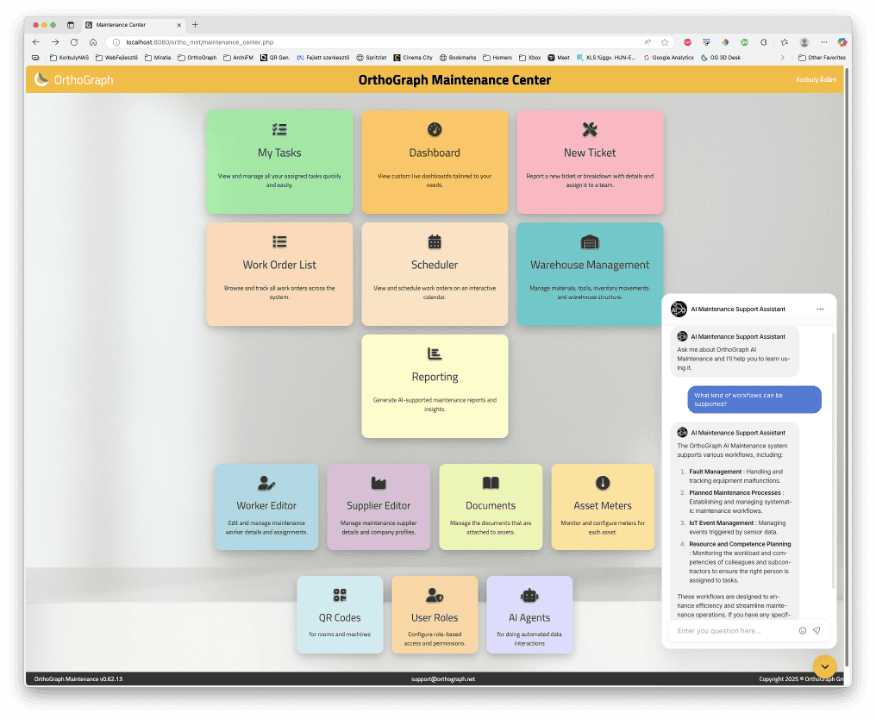
1. Dashboard and Visualization?
2. Work Orders
2.1. New Ticket
Used to create new work orders by scanning a QR code. Previous tickets are also visible depending on the user’s permission level.
2.2. My tasks
Displays all tasks assigned to the logged-in user. Tickets are shown in daily and weekly views, prioritizing open tickets followed by the last three closed ones.
2.3. Work order list
Provides an overview of all tickets, with AI-powered filters for quick selection based on specified criteria.
2.4. Work Order Details
Each work order contains information such as location, equipment, submitter, issue description, timestamps, and includes AI suggestions based on the linked asset.
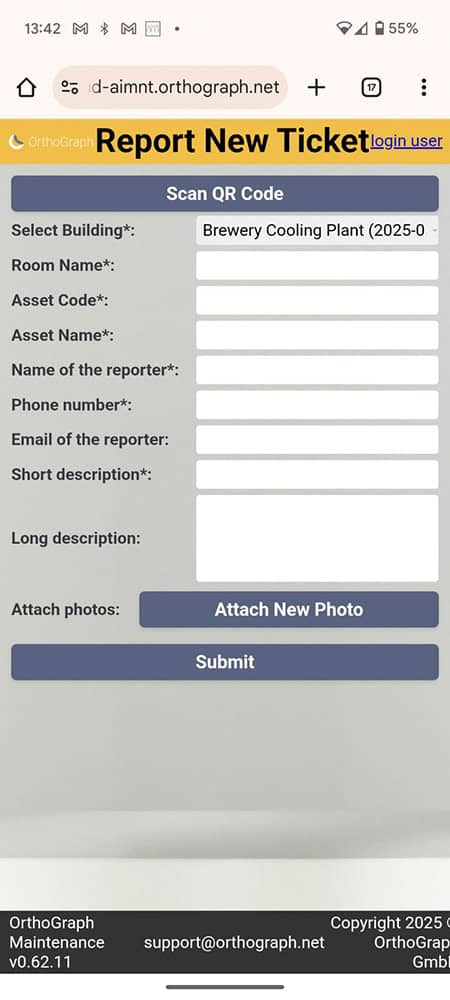
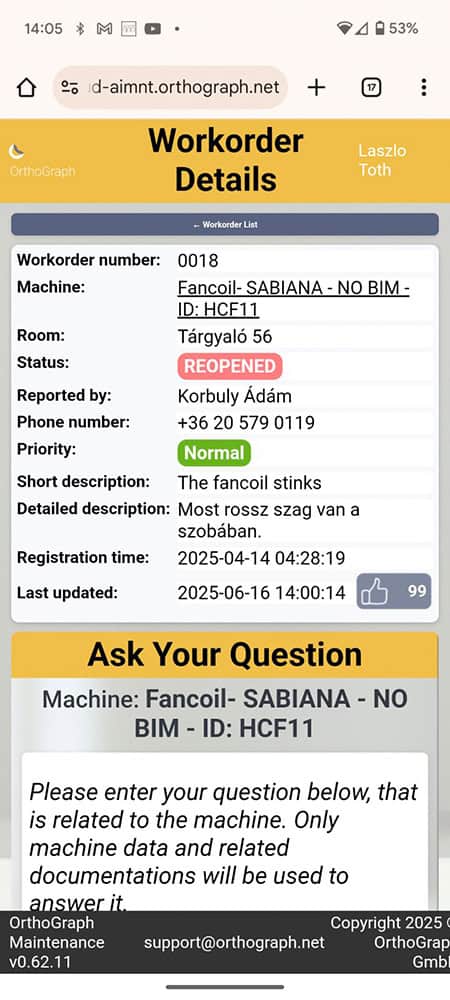
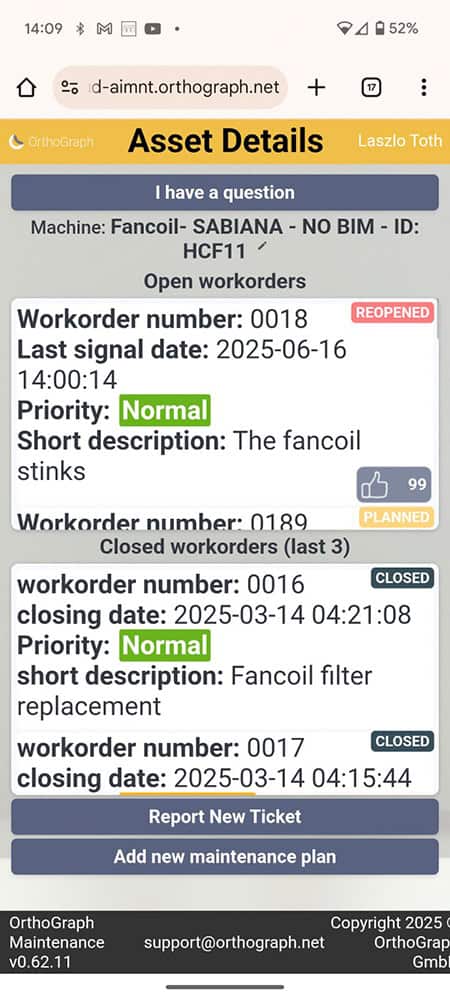
3. Assests
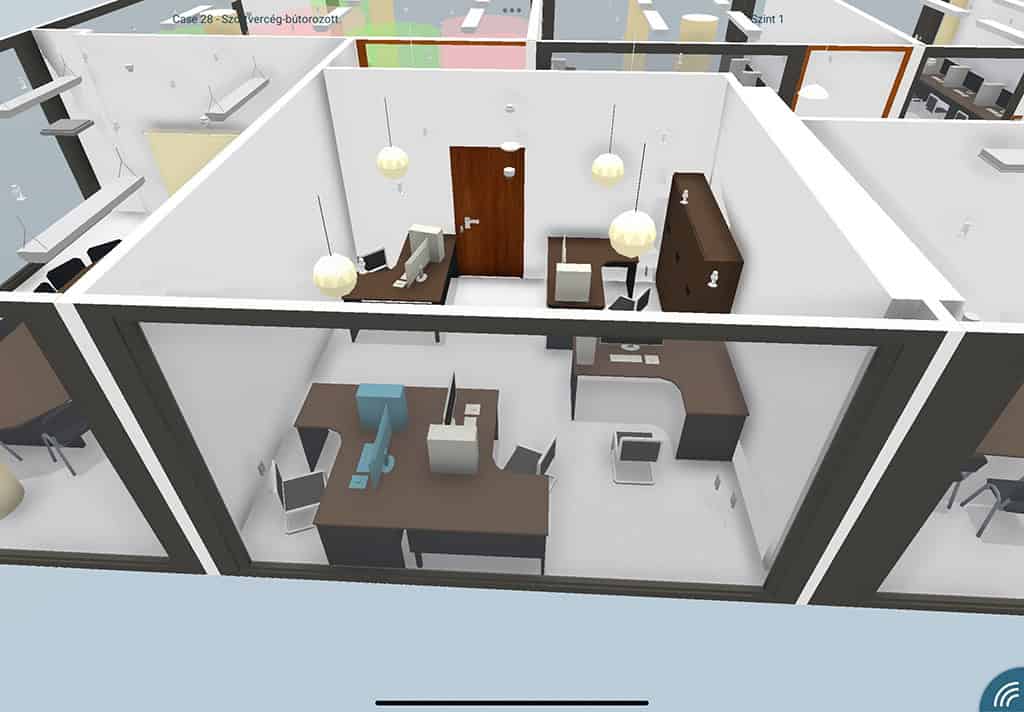
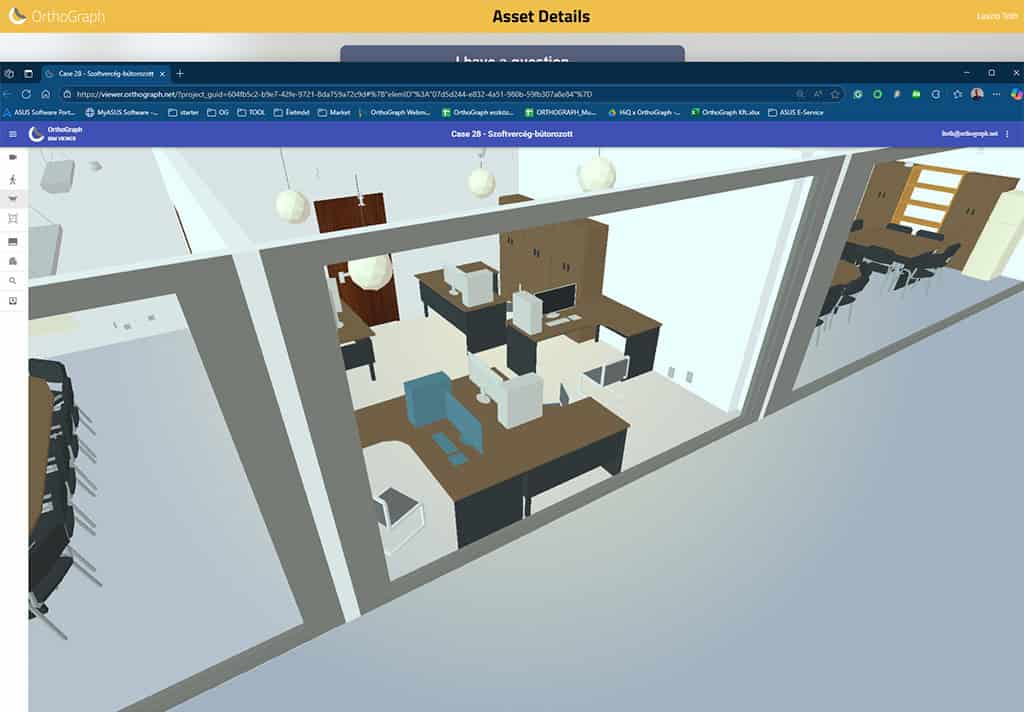
4. Work Order Planning
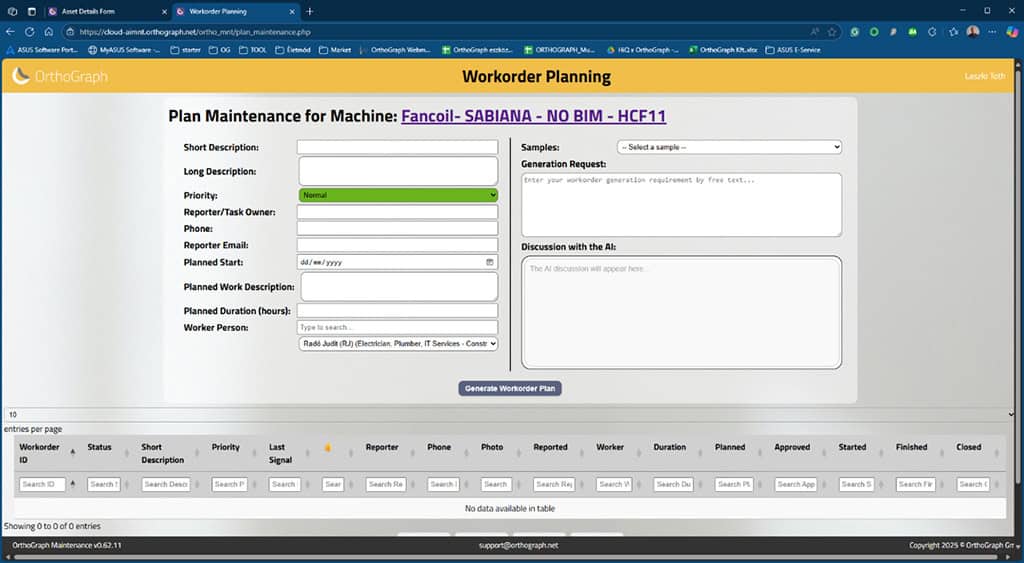
5. Inventory and Tools Tracking
6. Reporting
7. Supplementary Modules
7.1. Worker Editor
Used to manage employees: working hours, skills, departments, and permission levels:
7.2. Supplier Editor
Manages organizational affiliations and subcontractor assignments, supporting cost allocation and accountability.
7.3. Documents
The Document Manager stores and links maintenance-related documents (manuals, protocols, schematics, etc.) to assets. The AI engine uses these to assist troubleshooting and guide field staff with concrete suggestions.
7.4. QR Codes
Ensures every asset, location, or even shelf has a unique identifier, maintaining clarity between physical and digital layers of the system.
8. System block diagram
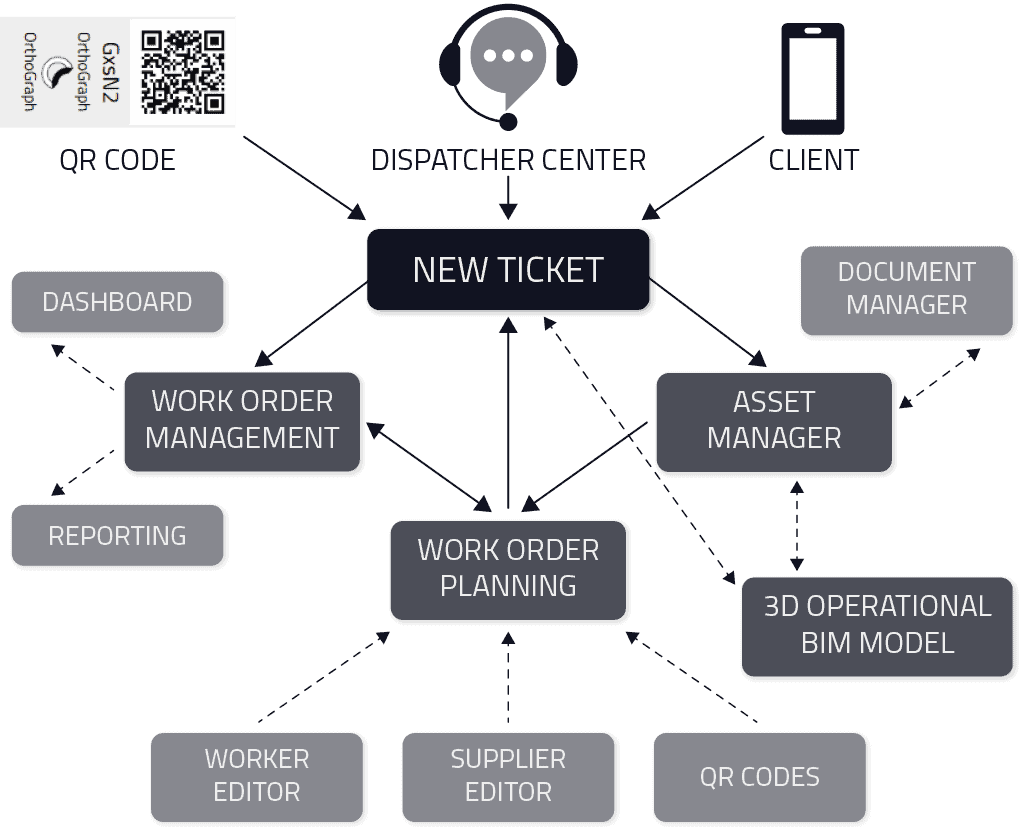
to our Newsletter
OrthoGraph

Contact us
Contact us
OrthoGraph GmbH
Gartenstrasse 7
Zug
Switzerland
6300
+ 41 (41) 5510150
9:00-18:00 Zurich Time
USA: +1 760 933 1550
UK : + 44 (20) 34119438
Other pages
Education
Rapid Survey Concept
Orthograph for Constructions
Historical Building Survey